The global differential-pressure level gauge market size is estimated to attain around USD 1,323.05 million by 2034 increasing from USD 702.84 million in 2024, growing at a CAGR of 6.53%.
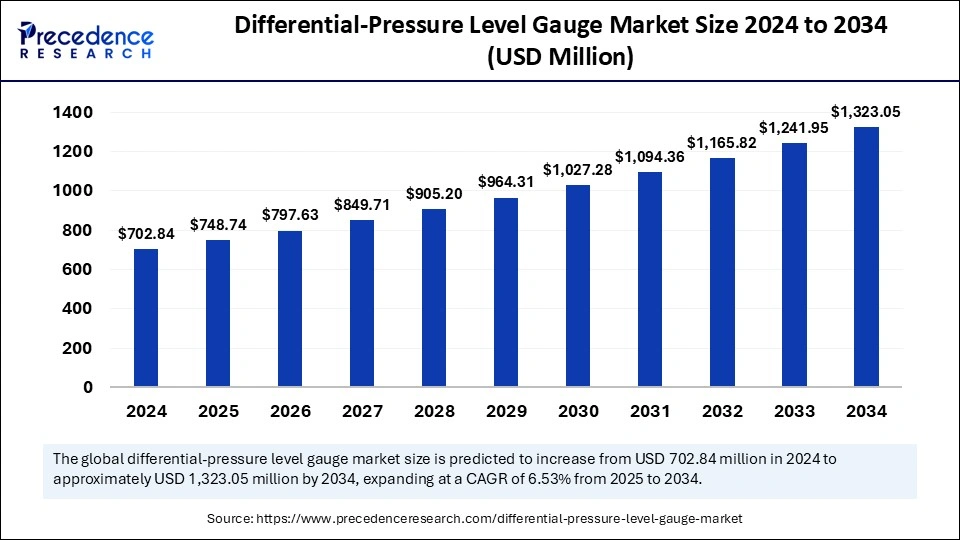
Get a Free Sample Copy of the Report@ https://www.precedenceresearch.com/sample/5760
Differential Pressure Level Gauge Market Key Points
-
North America was the leading region with a 34% market share in 2024.
-
Asia Pacific is predicted to be the fastest-growing region from 2025 to 2034.
-
The mechanical differential-pressure gauges segment dominated the market in 2024.
-
The magnetic differential-pressure gauges segment is projected to achieve the highest CAGR from 2025 to 2034.
-
The liquid level measurement segment held the largest share in 2024.
-
The gas level measurement segment is likely to expand significantly over the forecast period.
-
The oil and gas industry had the highest market share in 2024.
-
The food and beverage industry is set to experience the most rapid growth in the coming years.
Differential-Pressure Level Gauge: Overview and Functionality
A differential-pressure (DP) level gauge is a device used to measure the level of liquids or gases in tanks, vessels, and industrial processes. It operates based on the difference in pressure between two points—typically the top and bottom of a tank—to determine the liquid level. These gauges are widely used in industries such as oil and gas, chemical processing, water treatment, and food and beverage.
Working Principle
A DP level gauge measures the pressure difference between two points:
-
The high-pressure side is placed at the bottom of the tank, where the pressure is higher due to the liquid column.
-
The low-pressure side is positioned at the top, where the pressure is lower.
-
The difference between these pressures is used to calculate the liquid level.
Since the pressure is directly related to the height of the liquid column, the gauge provides an accurate level reading, even in sealed or pressurized tanks.
Types of Differential-Pressure Level Gauges
-
Mechanical Differential-Pressure Gauges – These use mechanical components, such as diaphragms, bellows, or bourdon tubes, to display the liquid level. They are durable and commonly used in harsh industrial environments.
-
Electronic Differential-Pressure Gauges – These use electronic sensors and transmitters to convert pressure readings into digital level measurements. They are more advanced and often integrated with industrial automation systems.
-
Magnetic Differential-Pressure Gauges – These gauges use a magnetic coupling mechanism to display level readings without direct contact with the liquid. They are suitable for hazardous or corrosive environments.
Applications of Differential-Pressure Level Gauges
-
Oil and Gas Industry – Used for monitoring liquid levels in storage tanks, separators, and pipelines.
-
Chemical Processing – Helps in maintaining accurate levels in reactors and chemical storage tanks.
-
Water Treatment – Used to measure levels in reservoirs, filtration units, and chemical dosing systems.
-
Food and Beverage – Ensures precise liquid level control in processing tanks and beverage production lines.
Advantages of Differential-Pressure Level Gauges
-
Reliable and Accurate – Provides precise level measurement even in pressurized tanks.
-
Suitable for Various Liquids – Works with corrosive, viscous, and high-temperature fluids.
-
Non-Intrusive Measurement – Magnetic and electronic versions allow level monitoring without direct contact with liquids.
-
Low Maintenance – Mechanical versions require minimal upkeep, making them cost-effective for long-term use.
The role of AI in the differential pressure level gauge market
AI is playing an increasingly vital role in the differential pressure level gauge market by improving accuracy, predictive maintenance, and automation. AI-driven algorithms enhance sensor performance by compensating for fluctuations in liquid density, temperature, and pressure, ensuring more precise level measurements. By integrating machine learning, AI enables real-time data analysis and anomaly detection, allowing industries to optimize processes and reduce manual monitoring efforts.
Furthermore, AI enhances predictive maintenance by analyzing data trends and predicting potential gauge failures before they occur. This reduces downtime and maintenance costs while improving overall system reliability. AI-powered automation also enables seamless integration of differential pressure level gauges with industrial IoT (IIoT) platforms, facilitating remote monitoring and control. As industries shift toward smart manufacturing, AI-driven differential pressure level gauges are expected to become an essential part of process optimization and efficiency.
Differential Pressure Level Gauge Market Overview
Differential pressure level gauges are widely used for liquid level measurement across various industries, ensuring accurate monitoring of fluid levels in tanks and processing systems. The market is growing due to the increasing need for efficiency and automation in industrial operations. Continuous technological advancements are further enhancing the performance and reliability of these gauges.
Differential Pressure Level Gauge Market Scope
Report Coverage |
Details |
Market Size by 2034 |
USD 1,323.05 Million |
Market Size in 2025 |
USD 748.74 Million |
Market Size in 2024 |
USD 702.84 Million |
Market Growth Rate from 2025 to 2034 |
CAGR of 6.53% |
Dominating Region |
North America |
Fastest Growing Region |
Asia Pacific |
Base Year |
2024 |
Forecast Period |
2025 to 2034 |
Segments Covered |
Product, Application, End-use Industry and Regions. |
Regions Covered |
North America, Europe, Asia-Pacific, Latin America, and Middle East & Africa |
Differential Pressure Level Gauge Market Dynamics
Market Drivers
Key drivers include the rising demand for real-time monitoring and automation in industries such as oil and gas, chemicals, and water treatment. Regulatory requirements for environmental safety and operational efficiency are also encouraging industries to adopt advanced level measurement technologies. The push for industrial digitalization further supports market expansion.
Market Opportunities
The advancement of AI and IoT-based smart sensors is creating new growth avenues in the market. AI-powered differential pressure level gauges can predict failures, reduce maintenance costs, and enhance efficiency. Additionally, increasing industrialization in emerging economies is driving demand for accurate and cost-effective level measurement solutions.
Market Challenges
One of the major challenges is the need for regular calibration and maintenance to ensure accurate readings. The initial investment in high-end differential pressure level gauges can be costly for small-scale industries. Moreover, extreme environmental conditions can affect the durability and performance of sensors over time.
Regional Insights
North America holds the largest market share, driven by technological advancements and the strong presence of industries relying on level measurement systems. Asia Pacific is expected to experience the highest growth due to rapid industrialization and infrastructure development. Europe remains a key region, benefiting from stringent regulations and a strong focus on process automation
Differential-Pressure Level Gauge Market Companies
- Emerson Electric Co.
- ABB Ltd.
- Honeywell International Inc.
- Siemens AG
- Yokogawa Electric Corporation
- Endress+Hauser Group
- Schneider Electric SE
- WIKA Alexander Wiegand SE & Co. KG
- KROHNE Group
- VEGA Grieshaber KG
- Dwyer Instruments, Inc.
- OMEGA Engineering, Inc.
- AMETEK, Inc.
- Ashcroft Inc.
- Fuji Electric Co., Ltd.
- Noshok, Inc.
- SOR Inc.
- Gems Sensors & Controls
- Brooks Instrument, LLC
- ABB Measurement & Analytics
Differential Pressure Level Gauge Market Recent Development
- In July 2024, ABB introduced the PGS300 as its first instrumentation product with an Environmental Product Declaration. This gauge pressure transmitter measures the pressure of liquids, gases, and steam, which is essential for the safety and efficiency of industries like chemicals, oil & gas, and hydrogen.
Segments Covered in the Report
By Product
- Mechanical Differential-pressure Gauges
- Electronic Differential-pressure Gauges
- Magnetic Differential-pressure Gauges
By Application
- Liquid Level Measurement
- Flow Measurement
- Gas Level Measurement
By End-use Industry
- Oil and Gas
- Chemical and Petrochemical
- Water and Wastewater Treatment
- Pharmaceutical
- Food and Beverage
- Power Generation
By Geography
- North America
- Europe
- Asia Pacific
- Latin America
- Middle East and Africa
Also Read: Biofouling Control Clean Sensor Market
Ready for more? Dive into the full experience on our website@ https://www.precedenceresearch.com/